
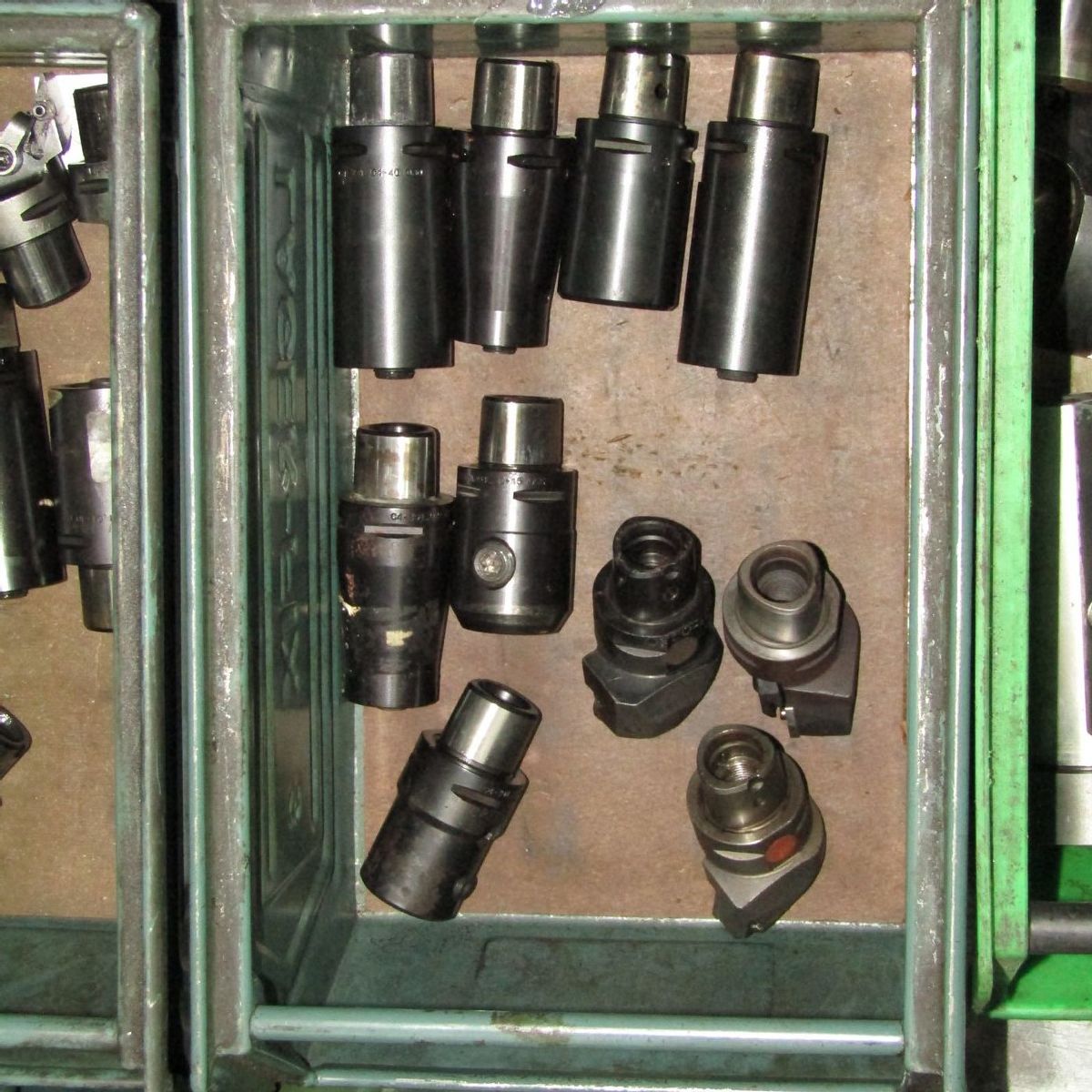
Make any centric or eccentric form desiredĤ, 6, or 8 edged, polygonal or free form with the EWS Multiform on the CNC turning/milling machinesįree forms that used to be impossible can now be made with EWS Multiform on turning/milling or machining centres.įor a six-edge outside the centre or a four-edge in the centre, additional processing steps such as reaming or eroding were necessary up until now. Sensor is based on BLE 4.2 technology (Bluetooth Low Energy) Data management, internal, external or in the cloud possible Sensor technology is open for communication with external interfaces Dynamic determination of load-dependent maintenance cycles Detect seal failure with "tsunami alarm" before machine damage occurs
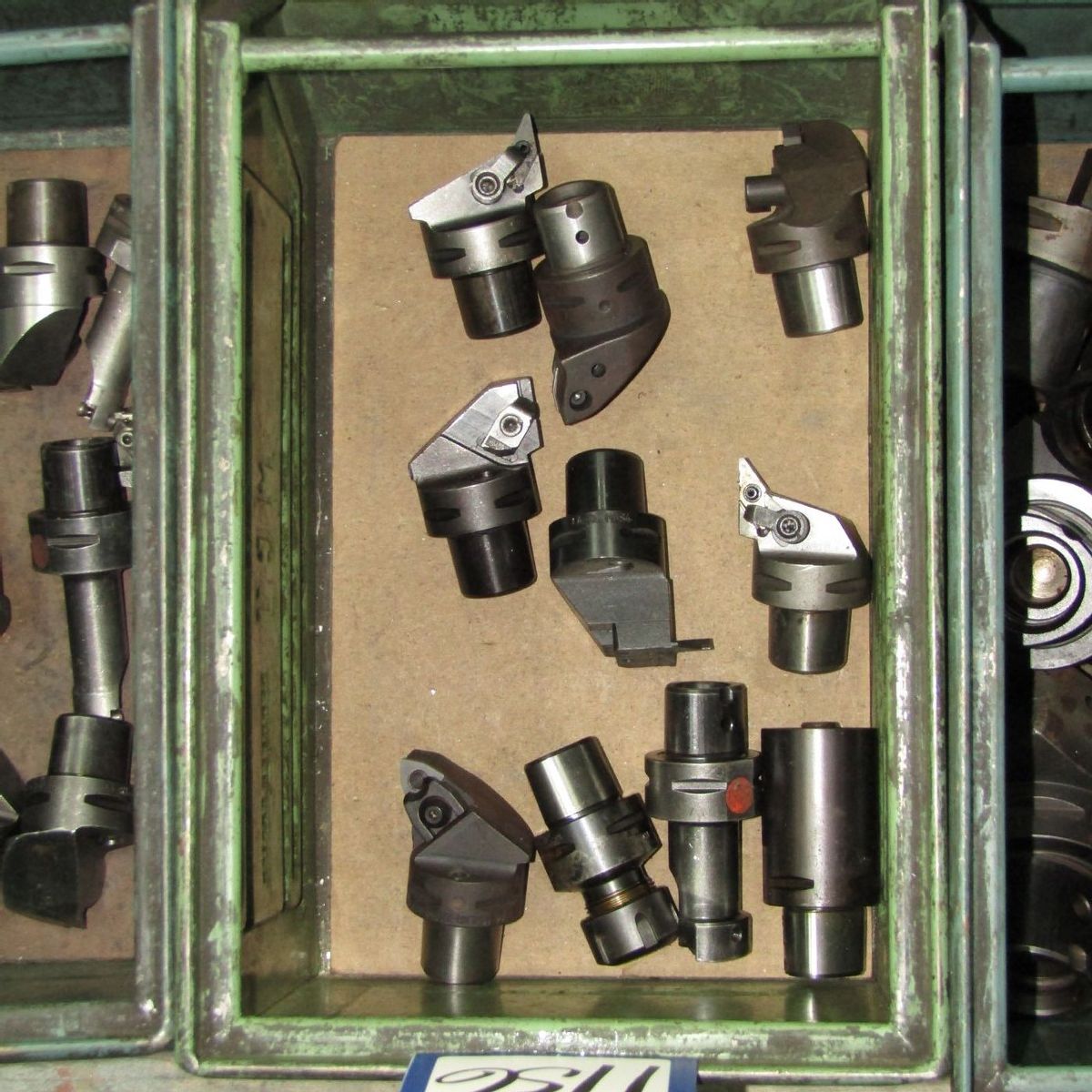
Avoidance of costly machine downtime thanks to intelligent tooling system The sensor system collects the following data: Currently, the electronics are in the field test and optimization phase and were presented to the public for the first time at EMO 2017. In the overall picture, EWS.CyberCon4 is a building block of the entire IoT concept of EWS. However, this is only part of the possibilities. Data can be read on a tablet or smartphone via an app. The digital concept is open also to competitors and cooperation partners in order to offer users as much standard as possible. With EWS.CyberCon4, EWS is entering the age of digital transformation. The digital view for capturing kinematic sequencesĮWS develops its own sensor technology as part of the Industry 4.0 concept. The system can be retrofitted to almost all tools supplied by EWS. The EWS-Adjust bar is provided with a fixed part with a counter screw opposite to eliminate the last play between the bar and pin. This is also only necessary once, providing there are no collisions. The tool that is used on the turret can be set using an external fixture. This task must be done once for all turret stations. The lower part of the eccentric is an expanding pin which is acted on by a threaded pin, thus securing the angle of rotation position. Together with an EWS setting pin, the pin can be aligned precisely with the machining position. For this purpose, EWS has developed an eccentric pin that is fitted into the same bore when the standard– pin is removed. There is only one way of doing this the pin on the turret must be aligned, and this must be done on the machine, preferably in the machining position. This consideration does not take account of the installation inaccuracies in the machine-tool.ĮWS has tackled this problem with its new EWS-Adjust system. If you consider that a PIN–position is 10μm offset in the Y-axis at a distance of 56 mm (in relation to the VDI bore), this amounts to as much as 0.03 mm on a normal drilling rod holder with an extension length of 100 mm.
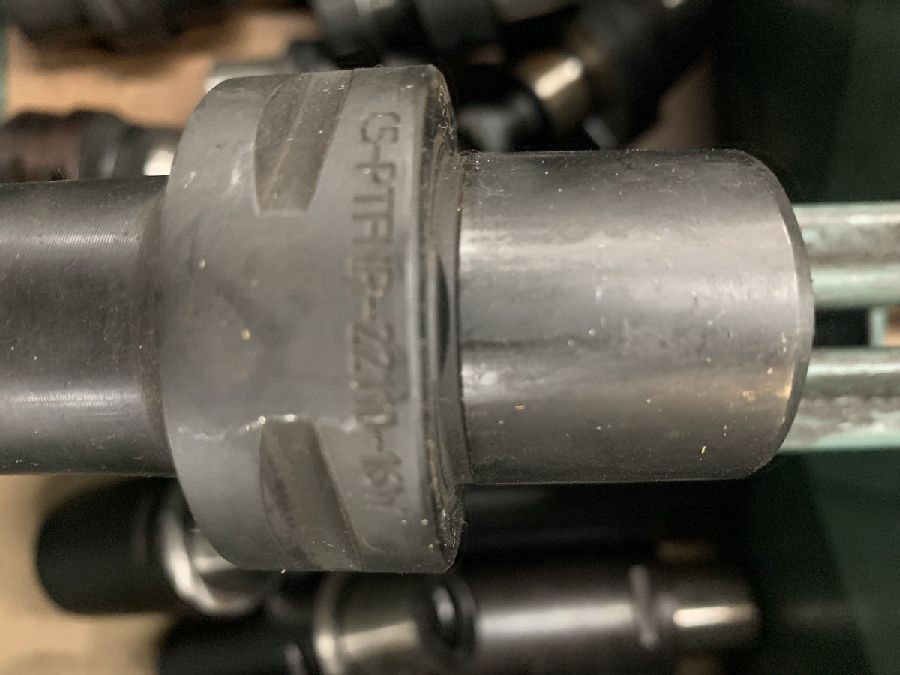
Irrespective of how the alignment on the pin is designed, it always takes time to achieve the setting, because the DIN pins that are generally used are never located exactly in position in the turret bore. The gains in travel speeds are eliminated by the enormously long setup times. However, this time-consuming calibration, especially when it comes to machines with 2 turrets (up to 28 tool stations) degrades the high fast motion speeds, rendering them insignificant. Incidentally, this solution can be retrofitted to many tool turrets at any time.Īligning using 2 screws on a pin in the turret is a widely used method. This is precisely what EWS has achieved with its Adjust system.
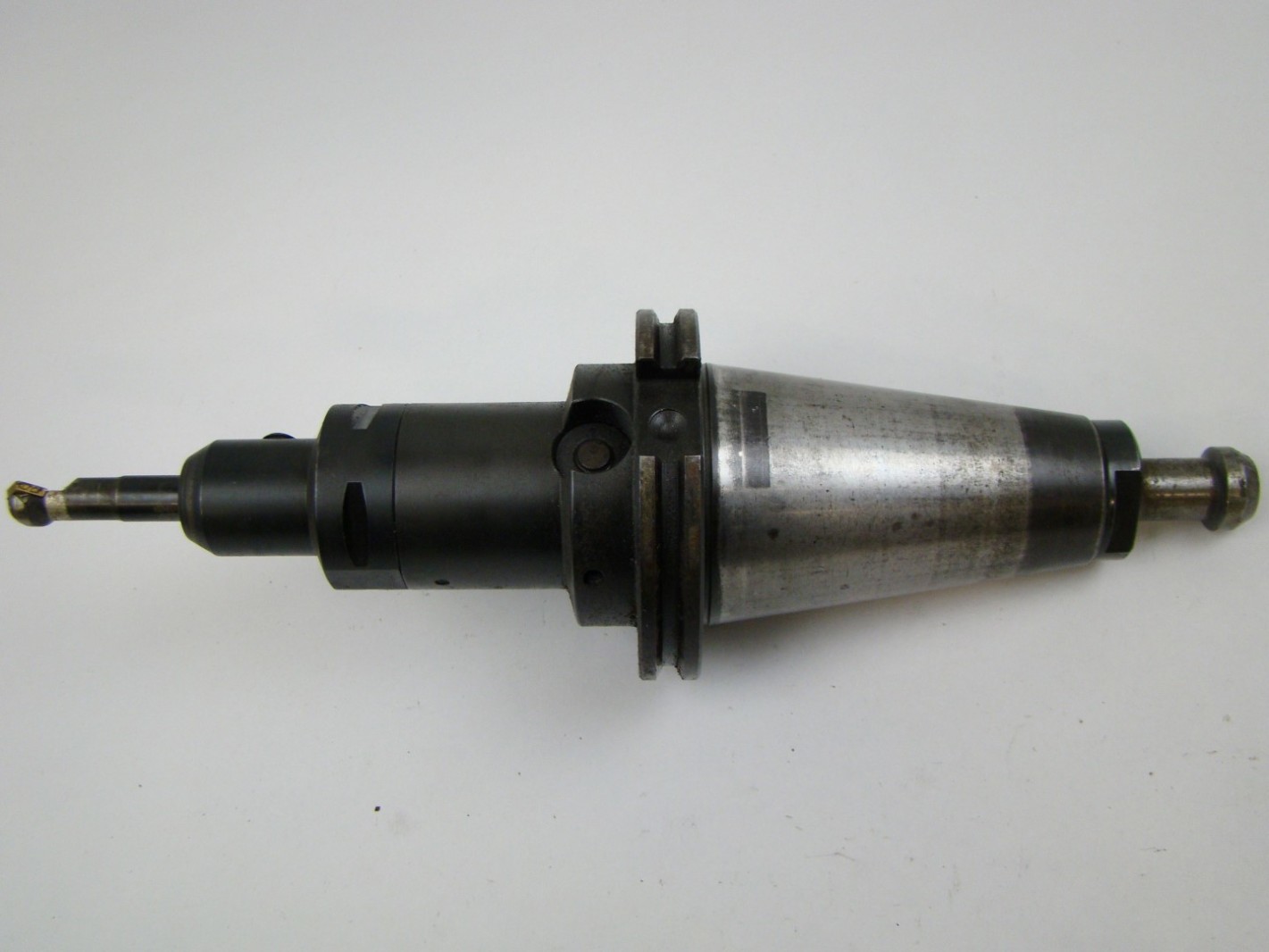
Time-consuming angle of rotation calibration is no longer required if this is guaranteed and implemented on all tool stations. The trick is to position the line of symmetry for the insertion hole in the turret congruent with that of the alignment pin. These were the fundamental requirements on EWS engineers… and they came up with the EWS-Adjust. „Give me a point on the turret disc that I can rely on, and aligning radial tools on the tool changer is a thing of the past.“ It is not quite so spectacular, but nevertheless closely related. „Give me a long enough lever and a place to stand, and I will move the Earth…
